Swipe to see the process
01
Cork Harvesting
The life cycle of cork as a raw material begins with extraction of the cork oak bark.
Harvesting takes place during the most active phase of growth of cork, between the middle of May or beginning of June until the middle or end of August.
It takes near 25 years for a cork oak trunk to start to produce cork and be profitable. Each trunk has to reach a circumference of about 70 cm when measured 1.3 metres above ground level. From then on, the cork can be harvested from the tree for on average 150 years.
The first harvest, which is known as “desbóia”, produces cork of a very irregular structure which is too hard to be easily handled.
This is the so-called virgin cork which will be used for applications other than cork stoppers (flooring, insulation etc.), since its quality is far from that necessary to manufacture stoppers.
Nine years later, the second harvest produces material with a regular structure, less hard, but still not suitable for cork stoppers – this is known as secondary cork.
It is from the third and subsequent harvests that the cork with the best properties is obtained, suitable for the production of quality corks, since its structure is regular with a smooth outside and inside. This is the so-called “amadia” or reproduction cork.
From then on, the cork oak will supply good quality cork every nine years for around a century and a half, producing, on average, 15 bark harvests throughout its life.
The harvesting of the cork oak is an ancient process that can only (and should) be done by experts known as “descortiçadores”. Manual skill and a lot of experience is required to avoid damaging the tree.
After the harvest, the cork planks are stacked in piles either in the forest or in yards at a factory. There they remain exposed to sun, wind and rain.
All the piles are constructed taking into account strict specific rules defined by the International Code of Cork Stopper Manufacturing Practice – ICCSMP, so as to allow the cork to stabilise.
The piles should be stacked on materials that do not contaminate the cork and prevent contact with the soil. Wood, for example, is expressly prohibited because it can transmit fungi.
During this seasoning period, the raw material matures and the cork stabilises.
According to the ICCSMP, the seasoning period for the planks should never be less than six months.
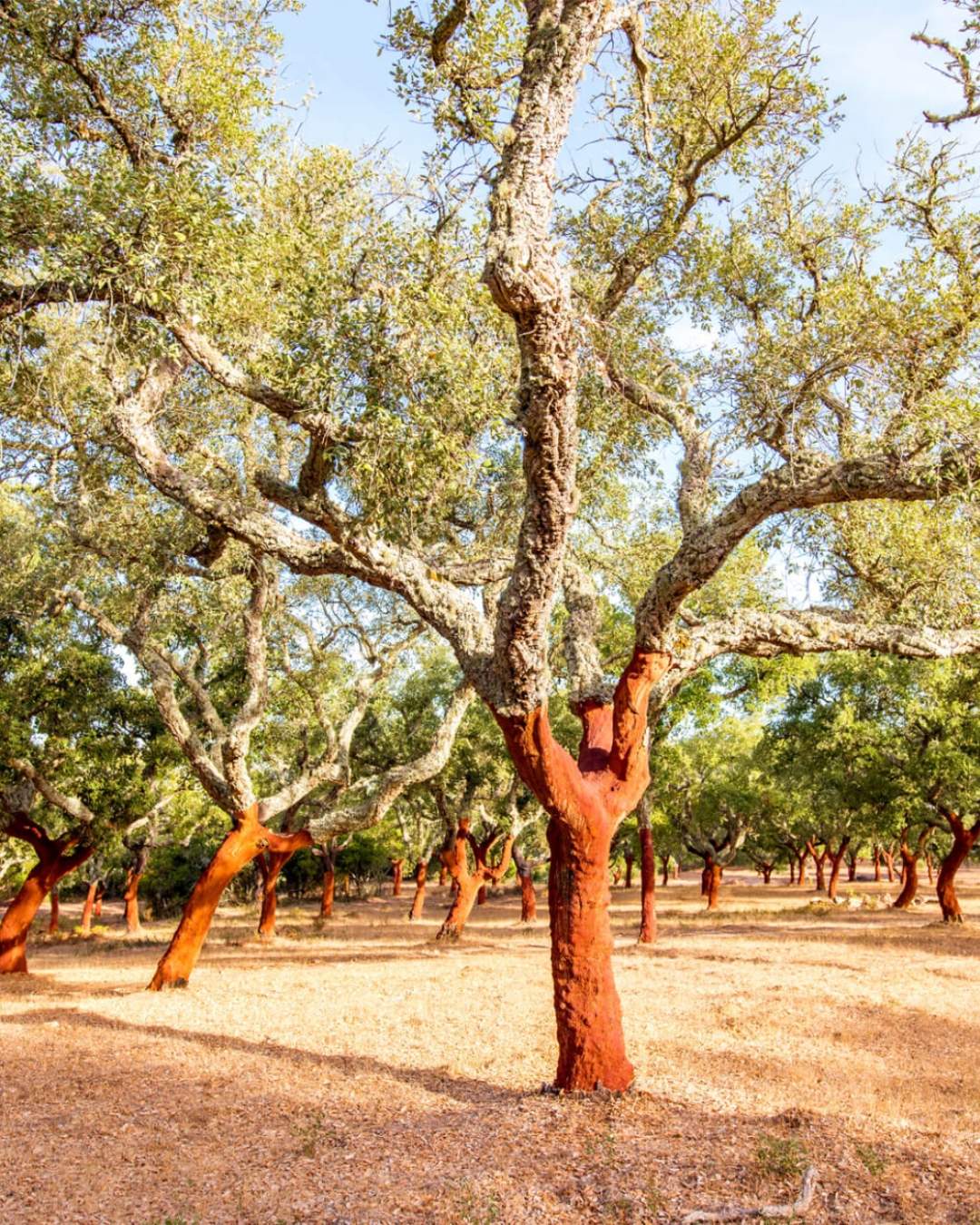
02
Boiling
Process that consists of total immersion of the cork planks in clean boiling water.
Its purpose is to clean cork, extract water-soluble substances, increase thickness, elasticity and soften cork.

03
Selection of Planks
and slicing
The edges of the planks are prepared and the corners trimmed before initial manual assessment takes place.
The planks are separated into quality categories based on their thickness, porosity and appearance.
Then, they are cut into strips with a width slightly greater than the length of the corks to be manufactured.
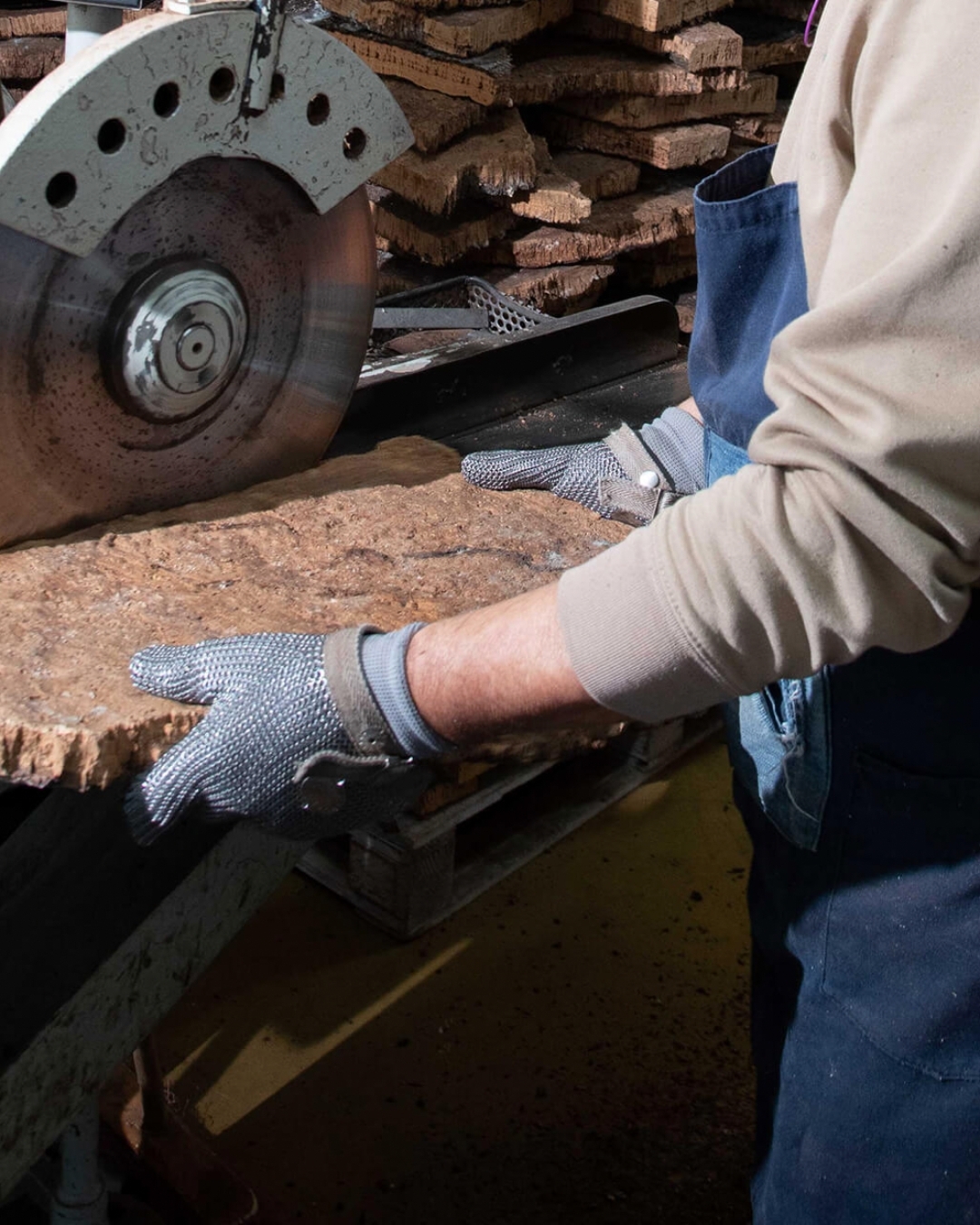
04
Punching
Punching is the name of the manual, semi-automatic or automatic process of perforating the strips of cork with a drill.
A cylindrical stopper is thus obtained within the defined dimensional limits.
All the waste from the punching stage are used for cork granulate.
Cork that is not directly used for top-of-the-range natural cork stoppers will be processed to make granulate for technical stoppers.
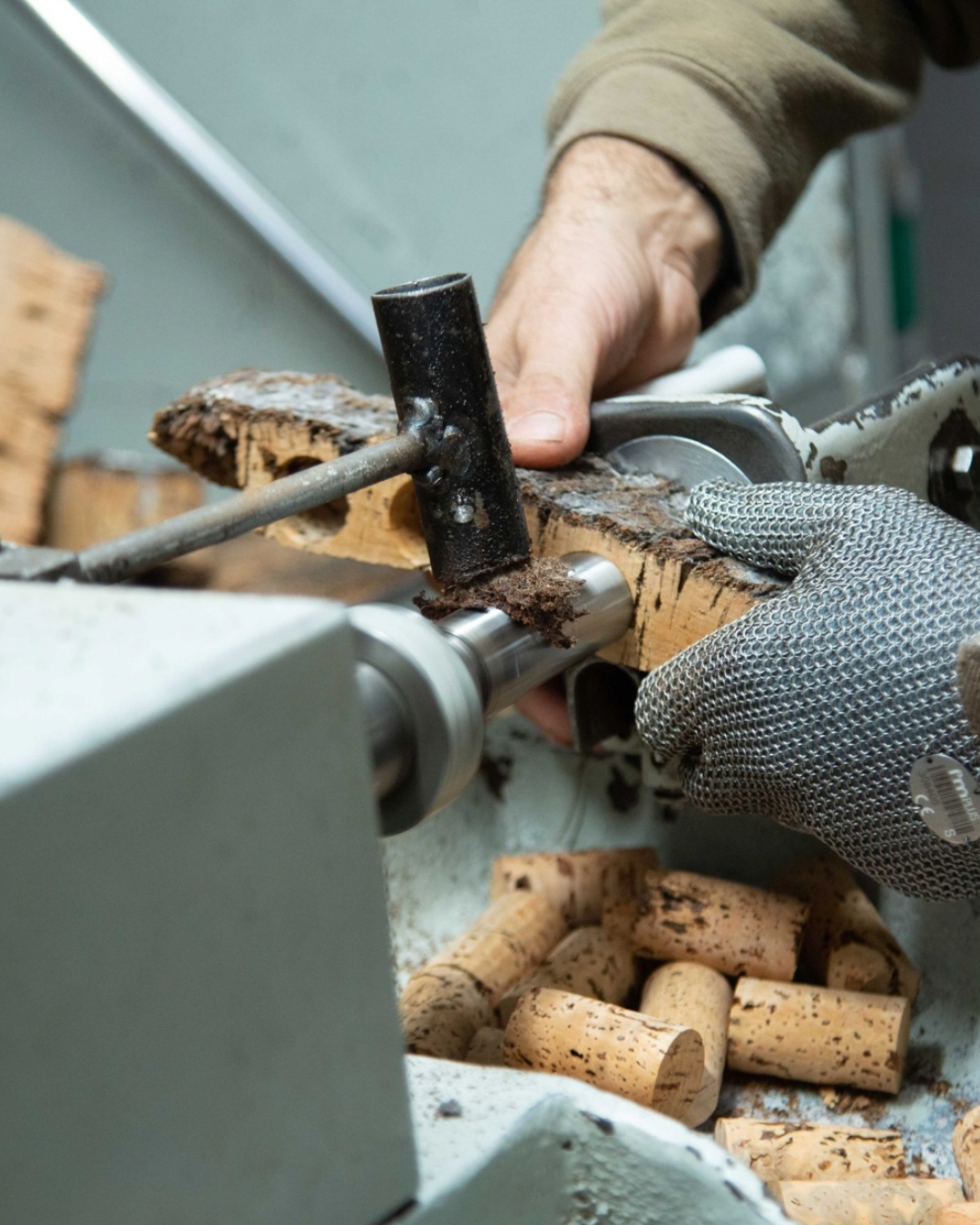
05
Rectification
After the punching, rectification is designed to obtain previously specified final dimensions and to regularise the surface of the stopper.
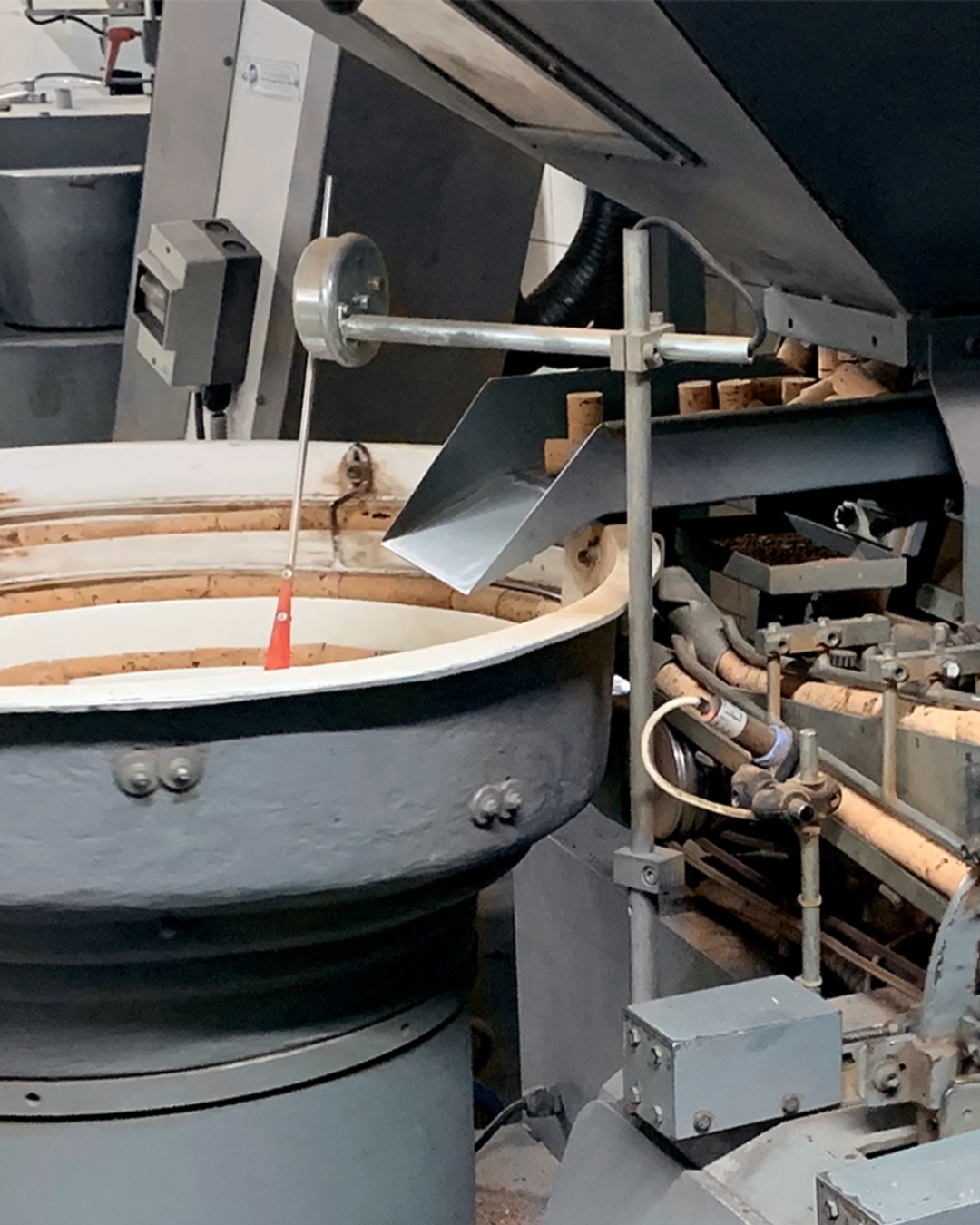
06
Selection
This operation designed to separate the finished stoppers into different grades, which are determined by automatic scanning of their surface.
In some cases, selection is carried out visually and manually, relying on the human eye.
During this phase, in addition to establishing quality classes, defective stoppers are eliminated.
In the generalized classification, it is common to find categories defined with the following names, according to visual criteria: Flor; Extra; Superior; 1st, 2nd, 3rd, 4th, 5th.
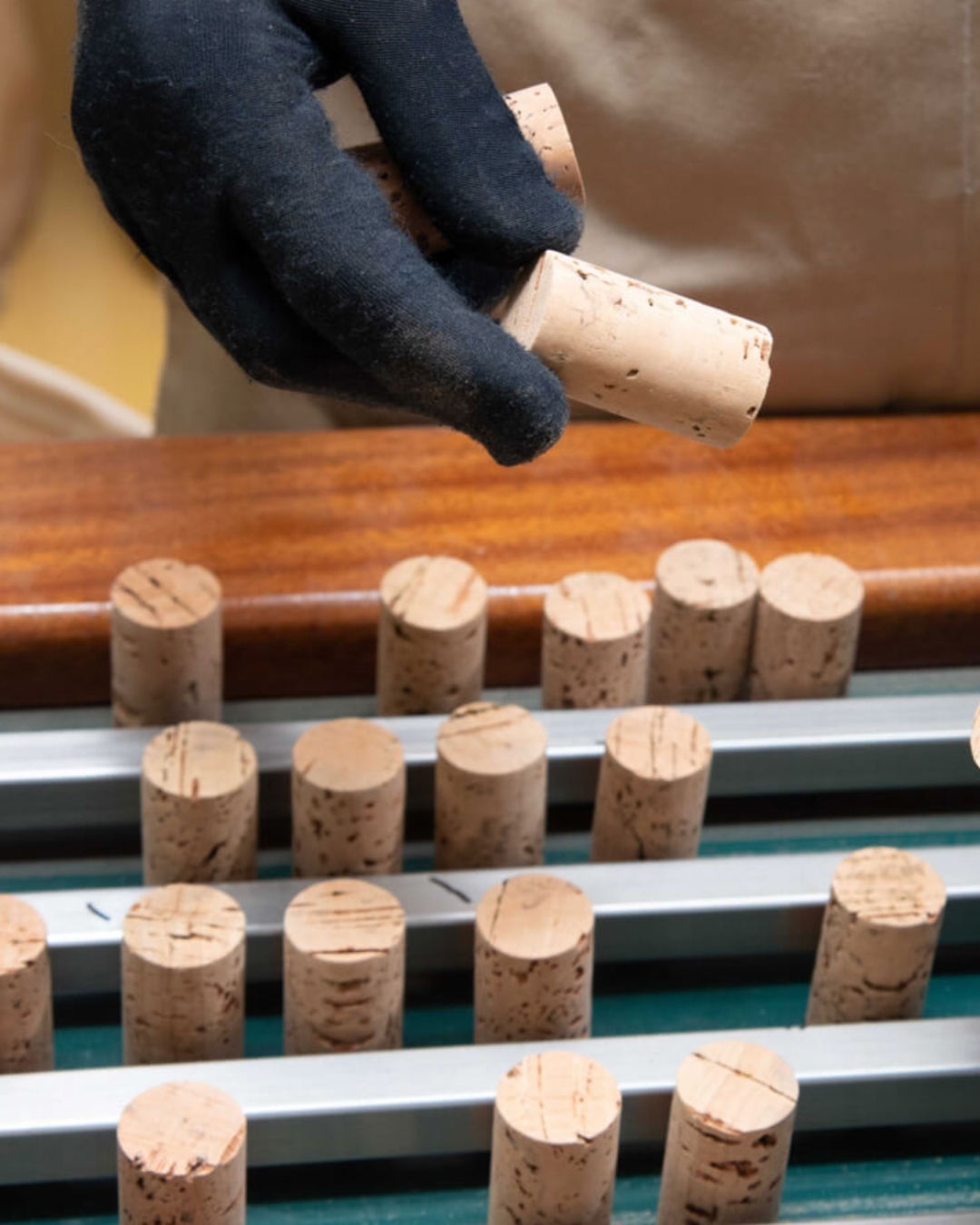
07
Cork Washing
The stoppers are washed after rectification . This cleans and disinfects the stoppers.
After washing/disinfection, the moisture content of the stoppers is stabilized, ensuring optimal sealing performance while simultaneously reducing microbiological contamination.
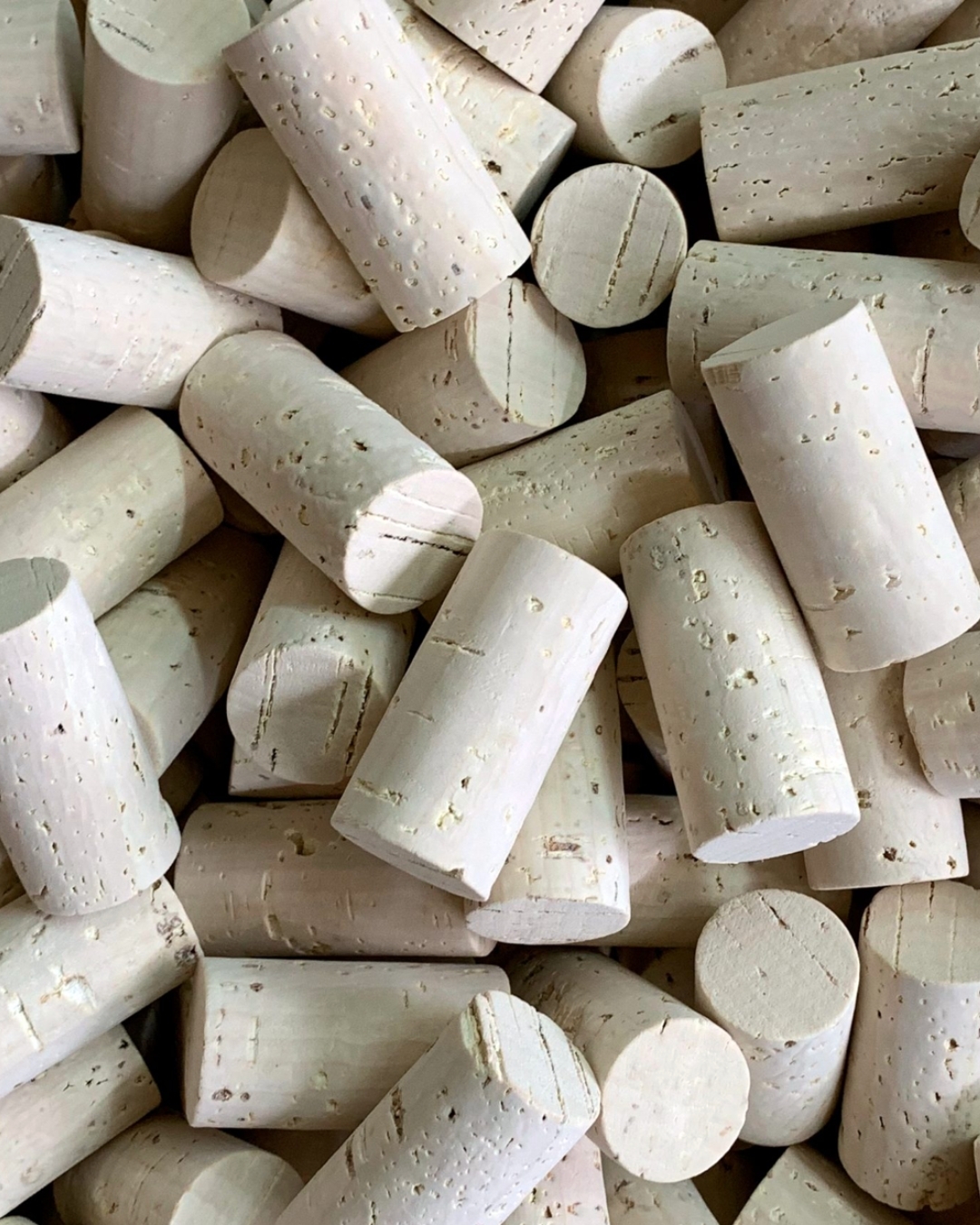
08
AQUACORK®
The process Aquacork ® consists in sealing the pores on the surface of cork stoppers (lenticels) with a mixture of cork dust obtained from the correction of natural cork stoppers.
Currently, a water-based glue is also used in this process.
This process is used to improve:
· Improve the visual aspect of the stopper;
· Improve their performance.
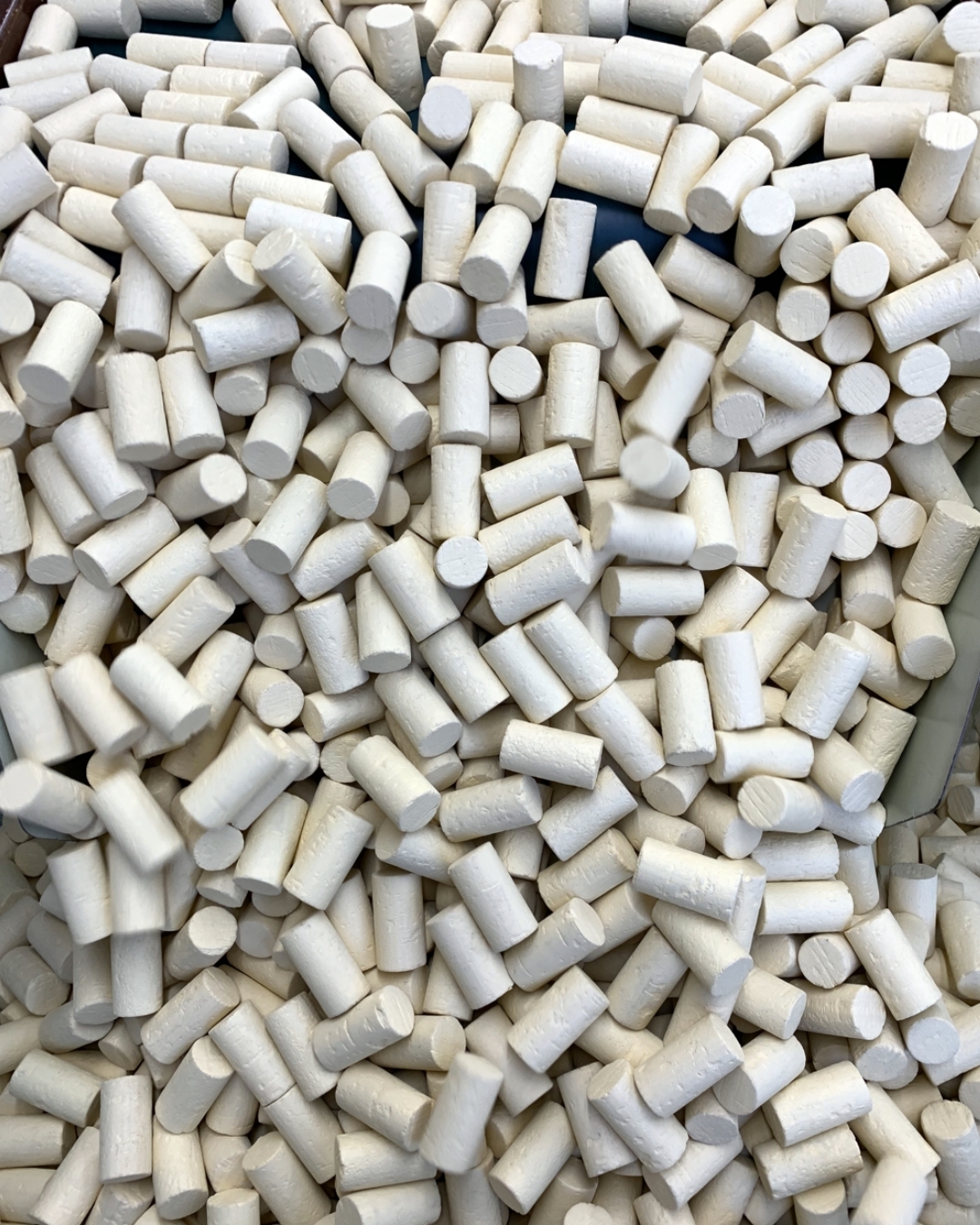
09
Marking
This operation is carried out according to customers specifications as to the type of marking to be applied.
Printing methods available are food-quality ink printing, heat marking or also laser marking.
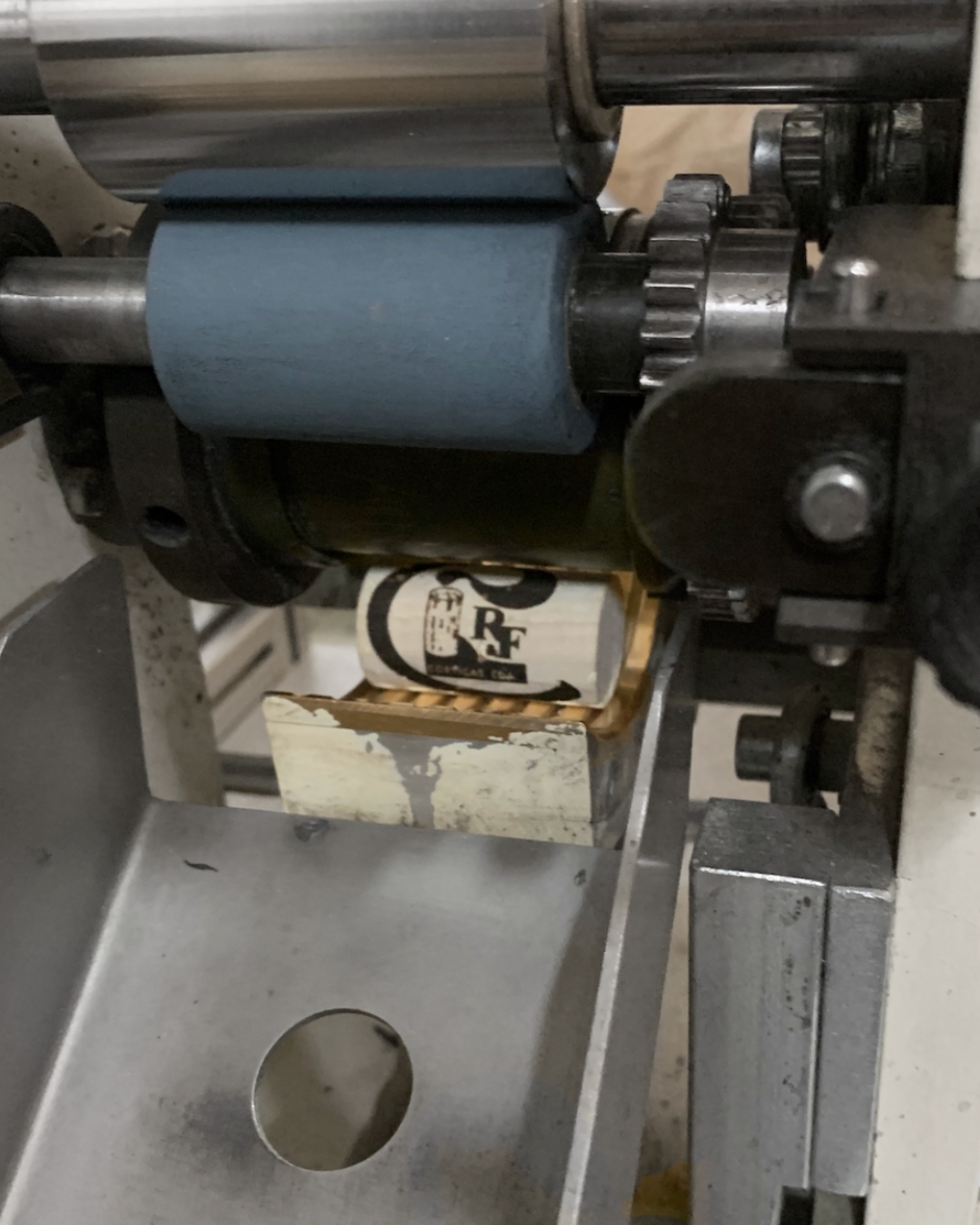
10
Surface Treatment and Packaging
The manufacturing process of cork stoppers ends with surface treatment. At this stage, a thin protective film is added to the corks, which facilitates bottling, sealing and cork extraction.
Once their production is finished, the stoppers are packed in plastic bags with SO2 (sulfur dioxide), a gas that blocks microbiological proliferation. Only then, the stoppers are transported to the bottling company to be used as closures for wine or spirits.
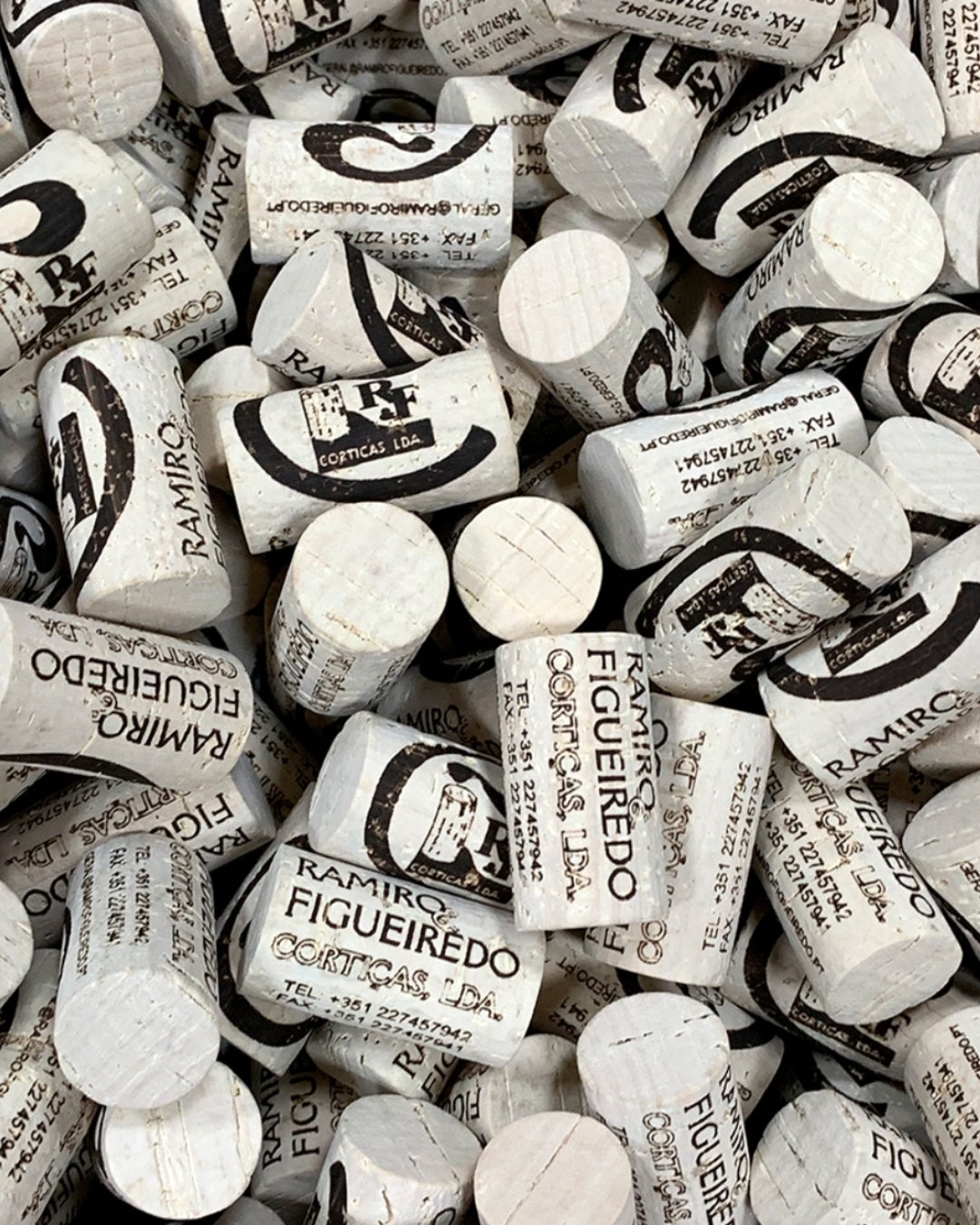
01
Cork Harvesting
The life cycle of cork as a raw material begins with extraction of the cork oak bark.
Harvesting takes place during the most active phase of growth of cork, between the middle of May or beginning of June until the middle or end of August.
It takes near 25 years for a cork oak trunk to start to produce cork and be profitable. Each trunk has to reach a circumference of about 70 cm when measured 1.3 metres above ground level. From then on, the cork can be harvested from the tree for on average 150 years.
The first harvest, which is known as “desbóia”, produces cork of a very irregular structure which is too hard to be easily handled.
This is the so-called virgin cork which will be used for applications other than cork stoppers (flooring, insulation etc.), since its quality is far from that necessary to manufacture stoppers.
Nine years later, the second harvest produces material with a regular structure, less hard, but still not suitable for cork stoppers – this is known as secondary cork.
It is from the third and subsequent harvests that the cork with the best properties is obtained, suitable for the production of quality corks, since its structure is regular with a smooth outside and inside. This is the so-called “amadia” or reproduction cork.
From then on, the cork oak will supply good quality cork every nine years for around a century and a half, producing, on average, 15 bark harvests throughout its life.
The harvesting of the cork oak is an ancient process that can only (and should) be done by experts known as “descortiçadores”. Manual skill and a lot of experience is required to avoid damaging the tree.
After the harvest, the cork planks are stacked in piles either in the forest or in yards at a factory. There they remain exposed to sun, wind and rain.
All the piles are constructed taking into account strict specific rules defined by the International Code of Cork Stopper Manufacturing Practice – ICCSMP, so as to allow the cork to stabilise.
The piles should be stacked on materials that do not contaminate the cork and prevent contact with the soil. Wood, for example, is expressly prohibited because it can transmit fungi.
During this seasoning period, the raw material matures and the cork stabilises.
According to the ICCSMP, the seasoning period for the planks should never be less than six months.
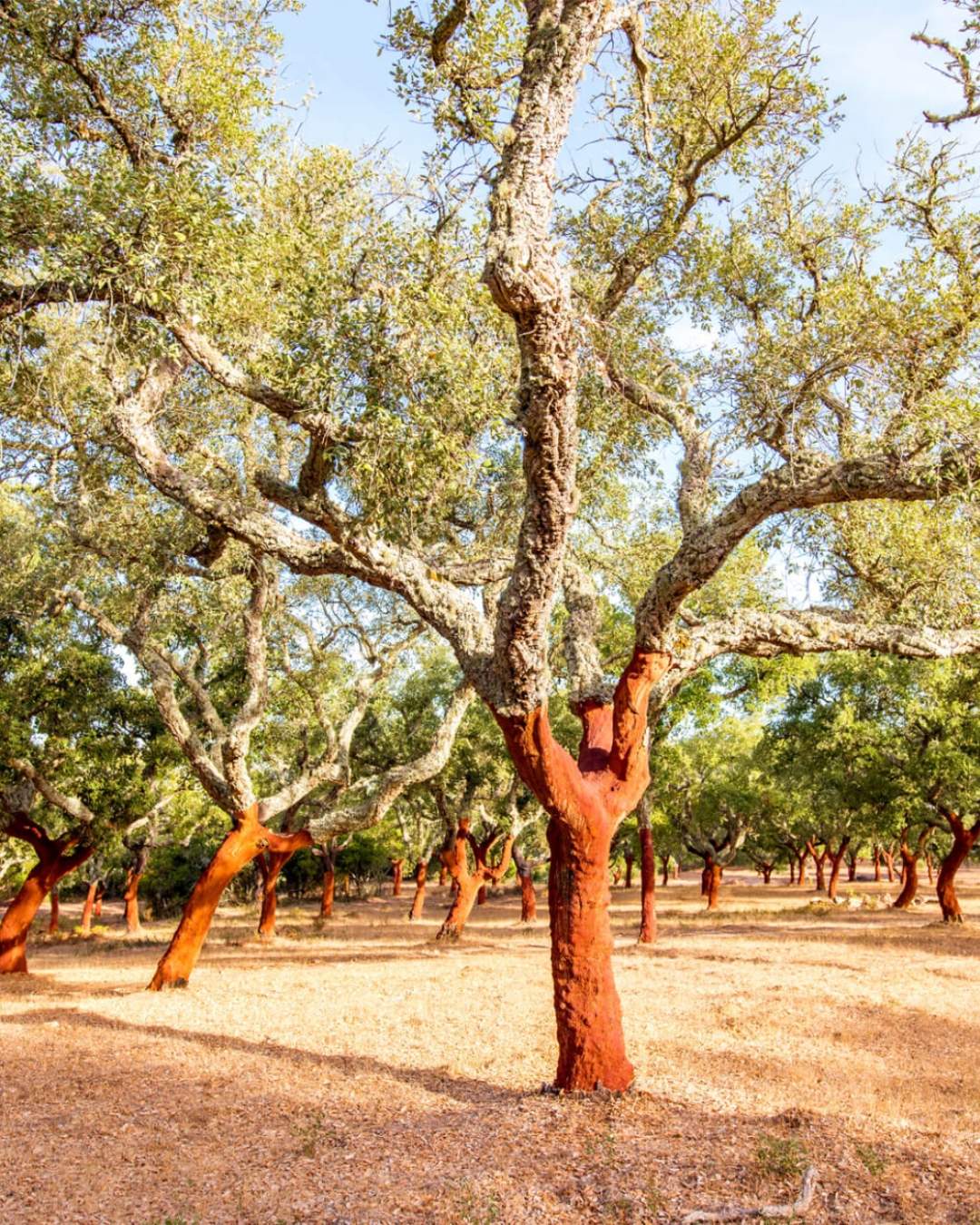
02
Boiling
Process that consists of total immersion of the cork planks in clean boiling water.
Its purpose is to clean cork, extract water-soluble substances, increase thickness, elasticity and soften cork.

03
Selection of Planks
and slicing
The edges of the planks are prepared and the corners trimmed before initial manual assessment takes place.
The planks are separated into quality categories based on their thickness, porosity and appearance.
Then, they are cut into strips with a width slightly greater than the length of the corks to be manufactured.
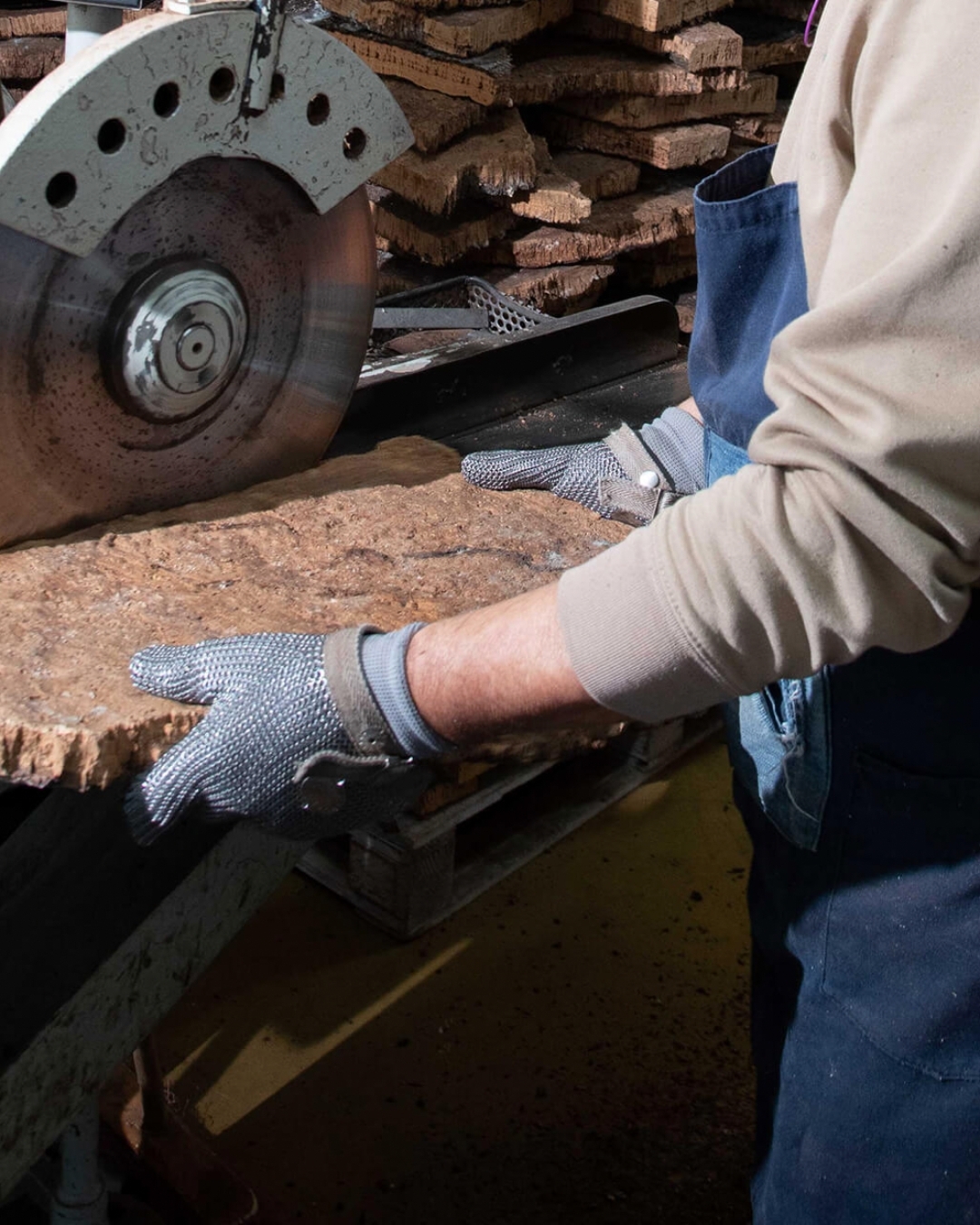
04
Punching
Punching is the name of the manual, semi-automatic or automatic process of perforating the strips of cork with a drill.
A cylindrical stopper is thus obtained within the defined dimensional limits.
All the waste from the punching stage are used for cork granulate.
Cork that is not directly used for top-of-the-range natural cork stoppers will be processed to make granulate for technical stoppers.
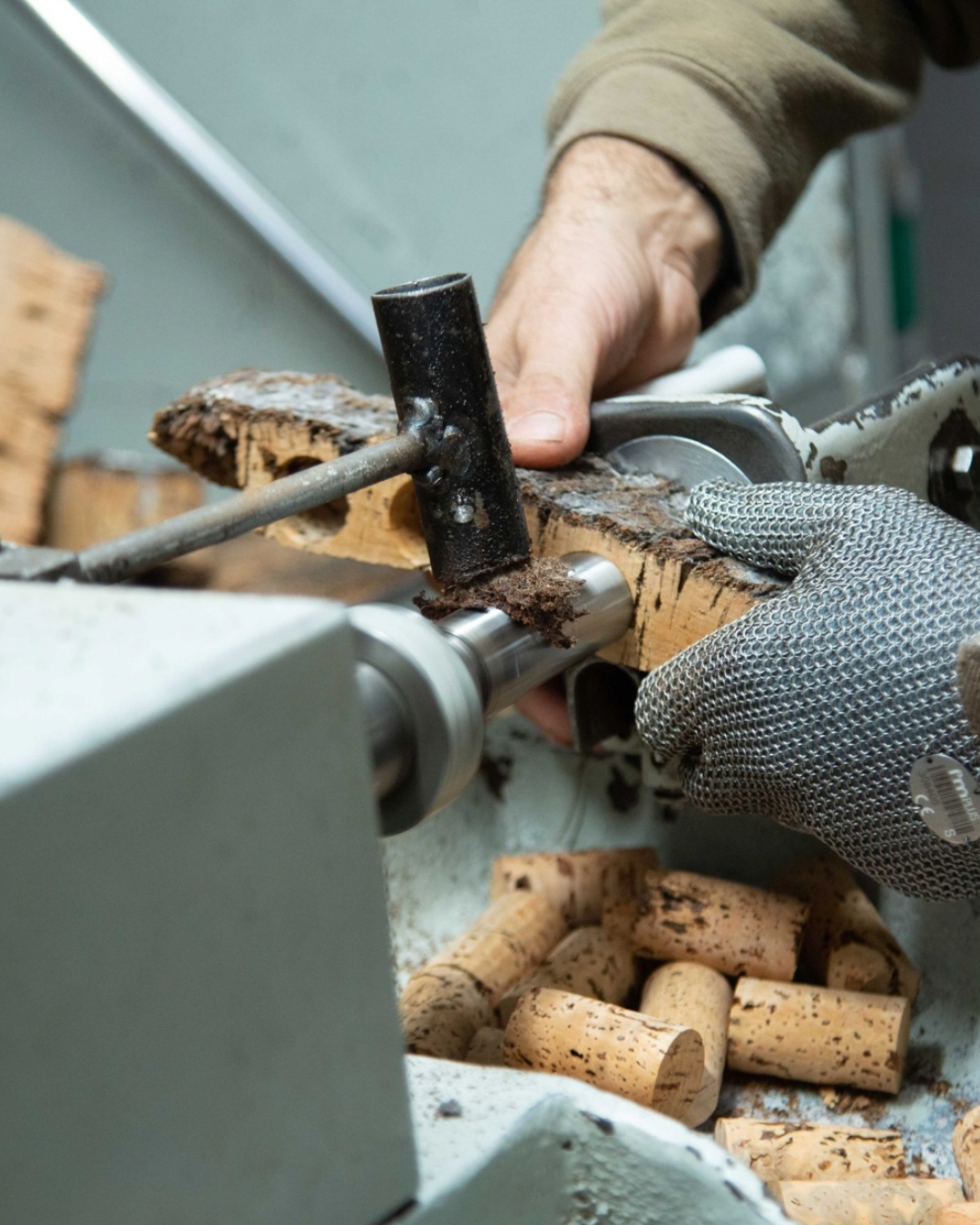
05
Rectification
After the punching, rectification is designed to obtain previously specified final dimensions and to regularise the surface of the stopper.
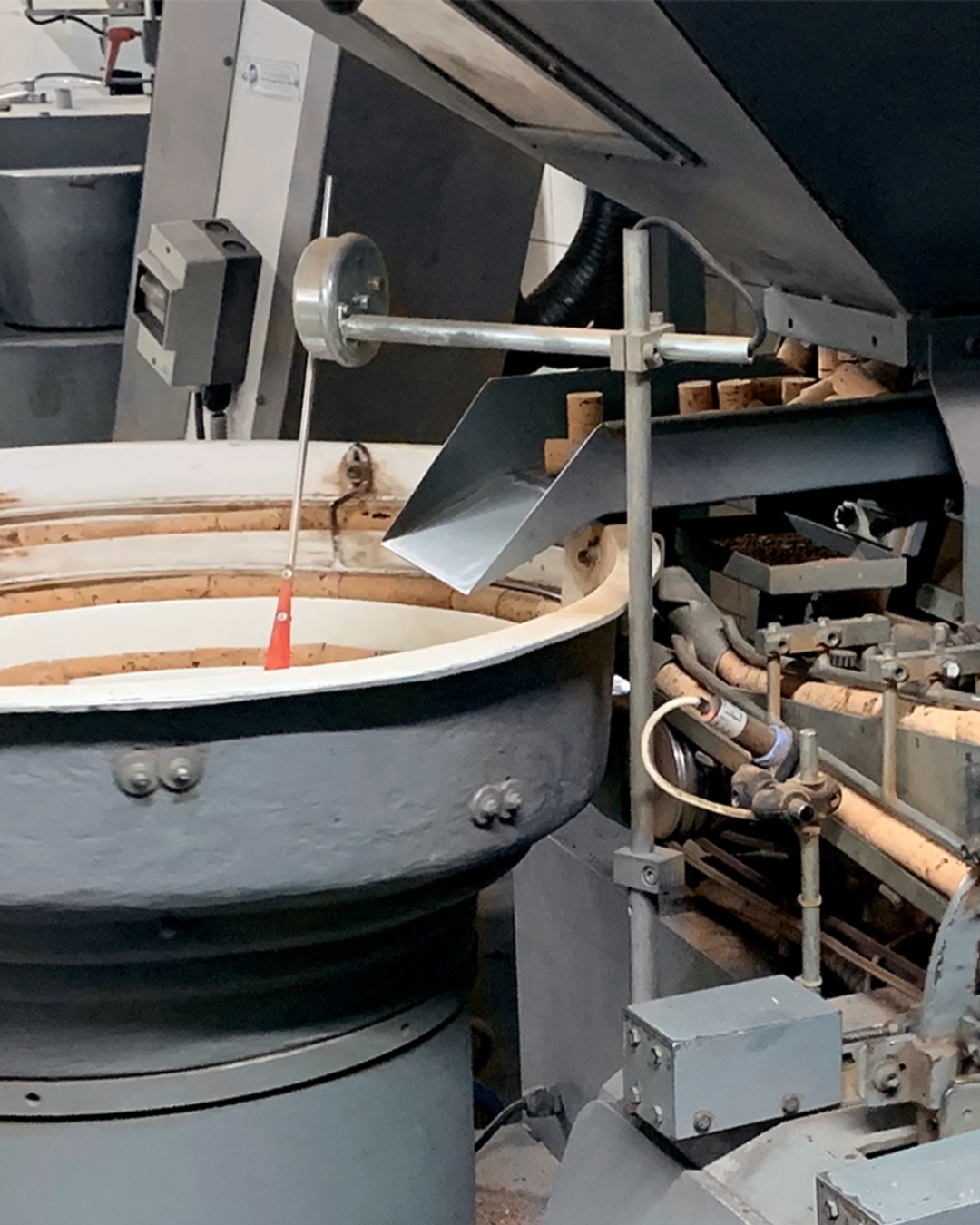
06
Selection
This operation designed to separate the finished stoppers into different grades, which are determined by automatic scanning of their surface.
In some cases, selection is carried out visually and manually, relying on the human eye.
During this phase, in addition to establishing quality classes, defective stoppers are eliminated.
In the generalized classification, it is common to find categories defined with the following names, according to visual criteria: Flor; Extra; Superior; 1st, 2nd, 3rd, 4th, 5th.
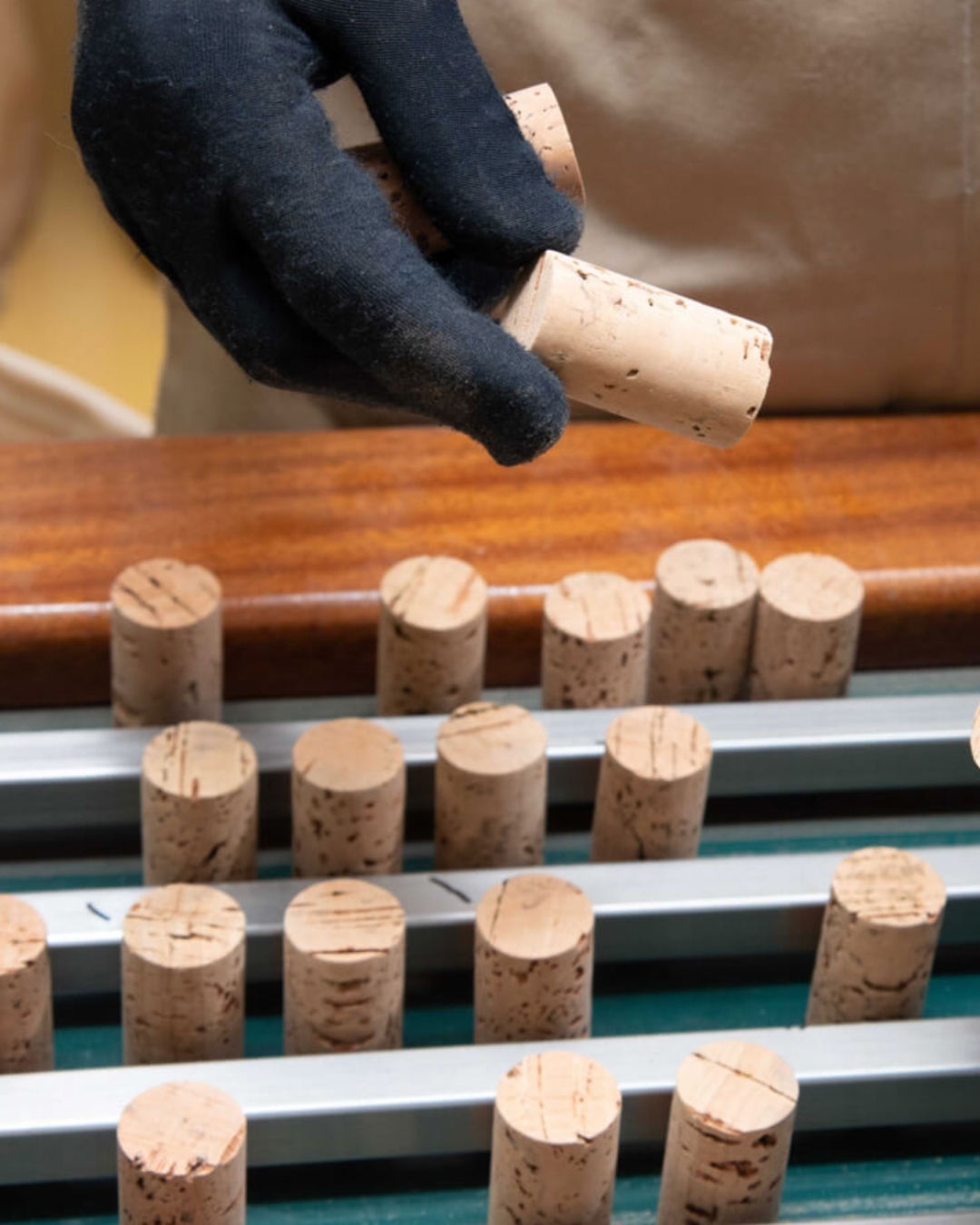
07
Cork Washing
The stoppers are washed after rectification . This cleans and disinfects the stoppers.
After washing/disinfection, the moisture content of the stoppers is stabilized, ensuring optimal sealing performance while simultaneously reducing microbiological contamination.
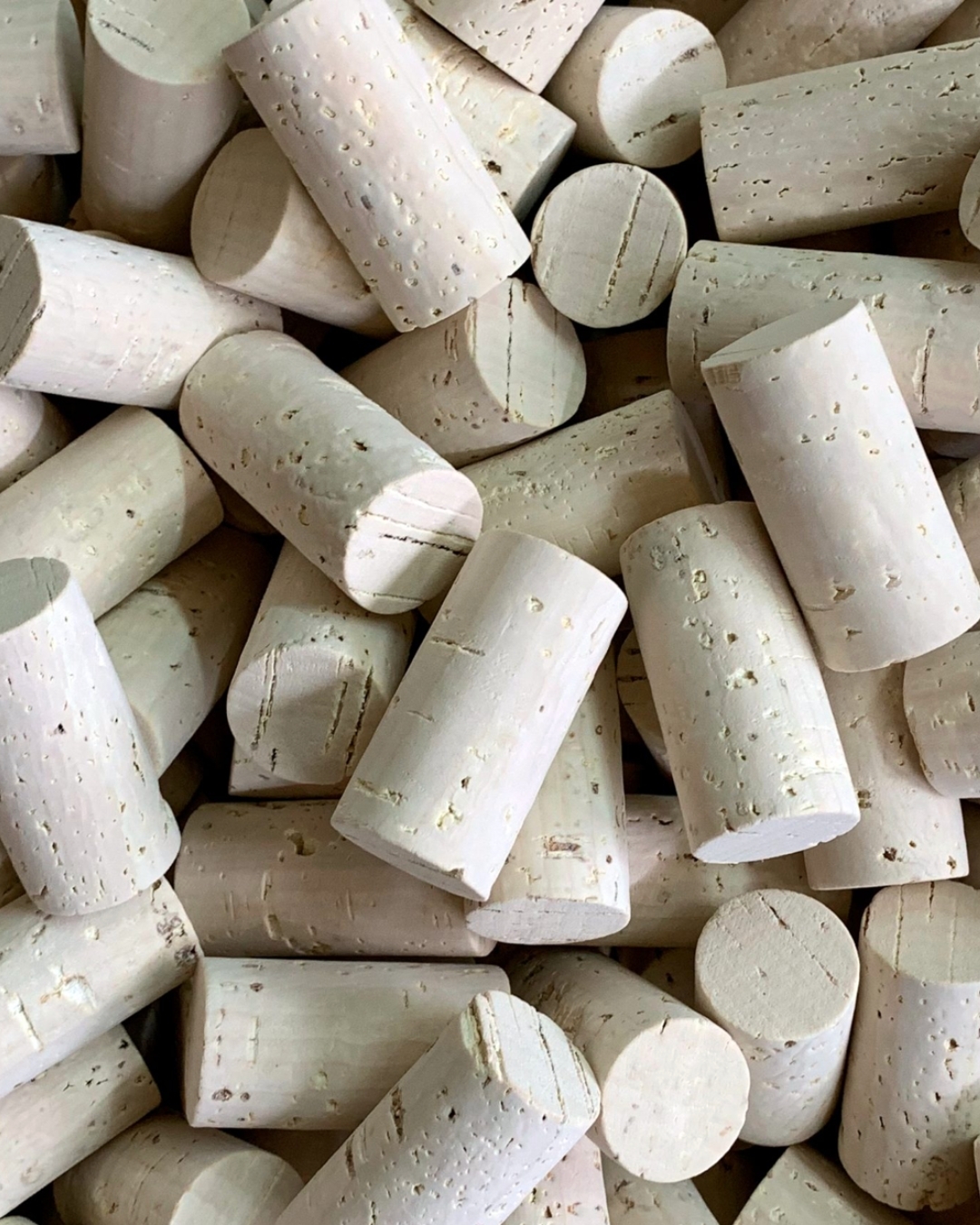
08
AQUACORK®
The process Aquacork ® consists in sealing the pores on the surface of cork stoppers (lenticels) with a mixture of cork dust obtained from the correction of natural cork stoppers.
Currently, a water-based glue is also used in this process.
This process is used to improve:
· Improve the visual aspect of the stopper;
· Improve their performance.
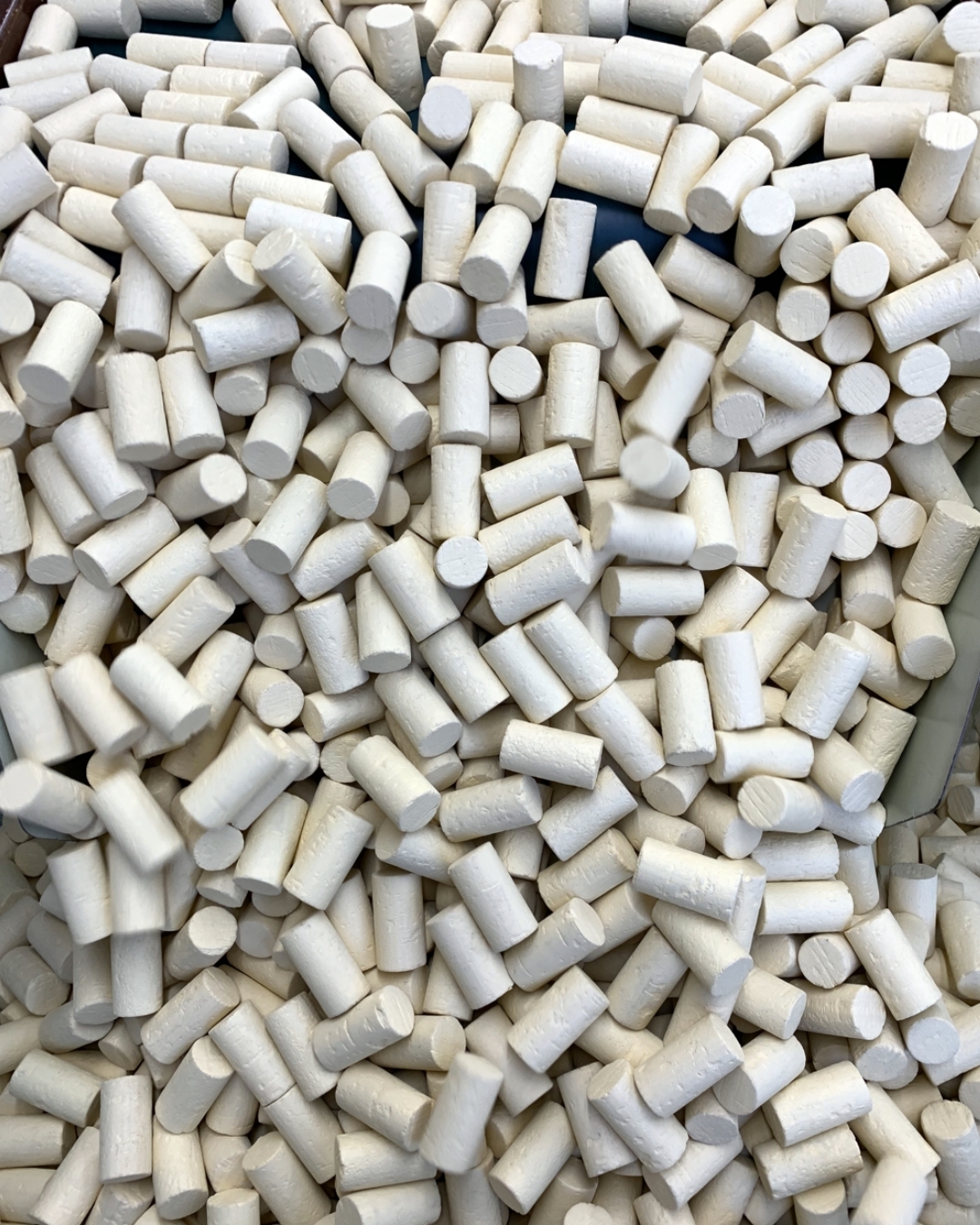
09
Marking
This operation is carried out according to customers specifications as to the type of marking to be applied.
Printing methods available are food-quality ink printing, heat marking or also laser marking.
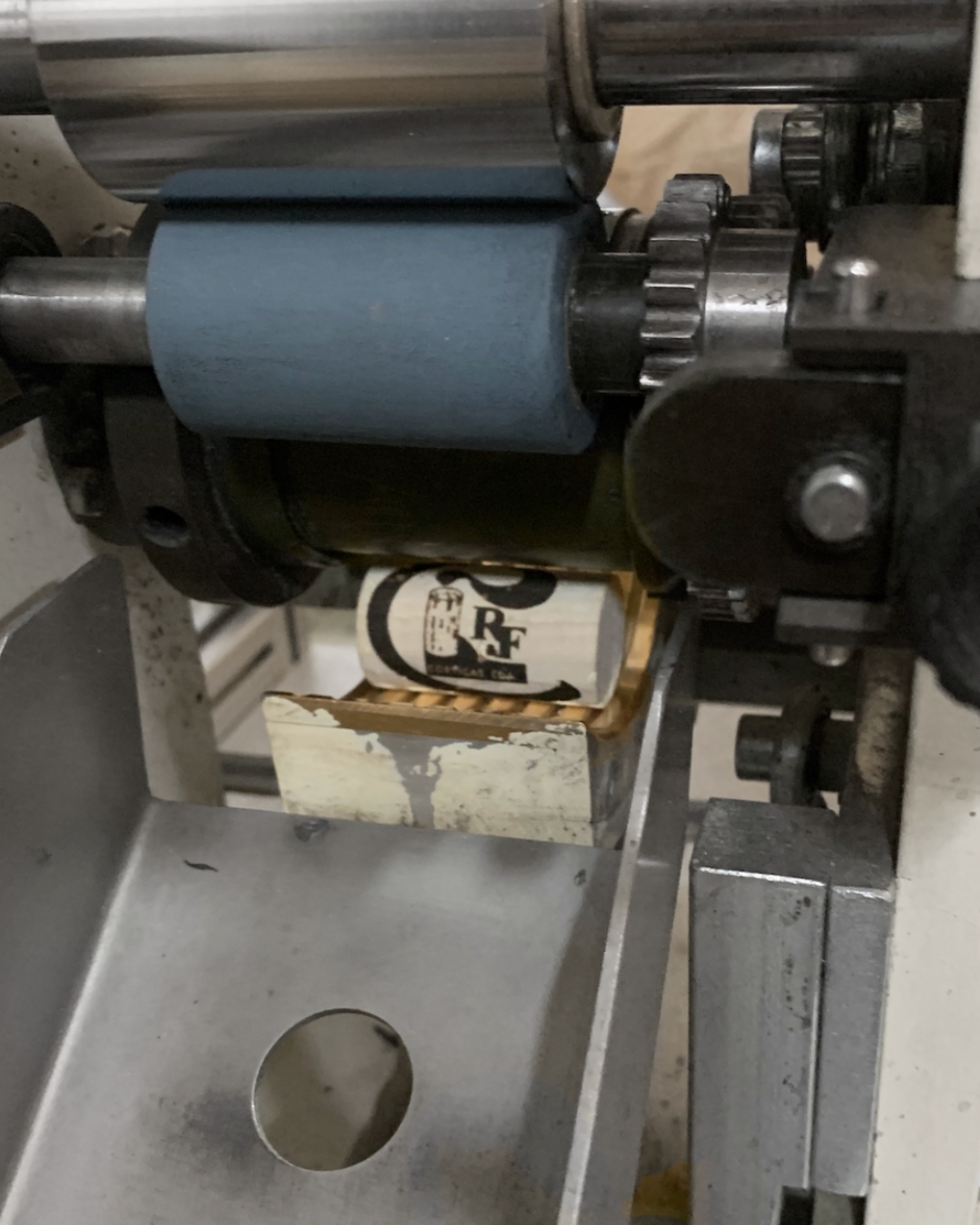
10
Surface Treatment and Packaging
The manufacturing process of cork stoppers ends with surface treatment. At this stage, a thin protective film is added to the corks, which facilitates bottling, sealing and cork extraction.
Once their production is finished, the stoppers are packed in plastic bags with SO2 (sulfur dioxide), a gas that blocks microbiological proliferation. Only then, the stoppers are transported to the bottling company to be used as closures for wine or spirits.
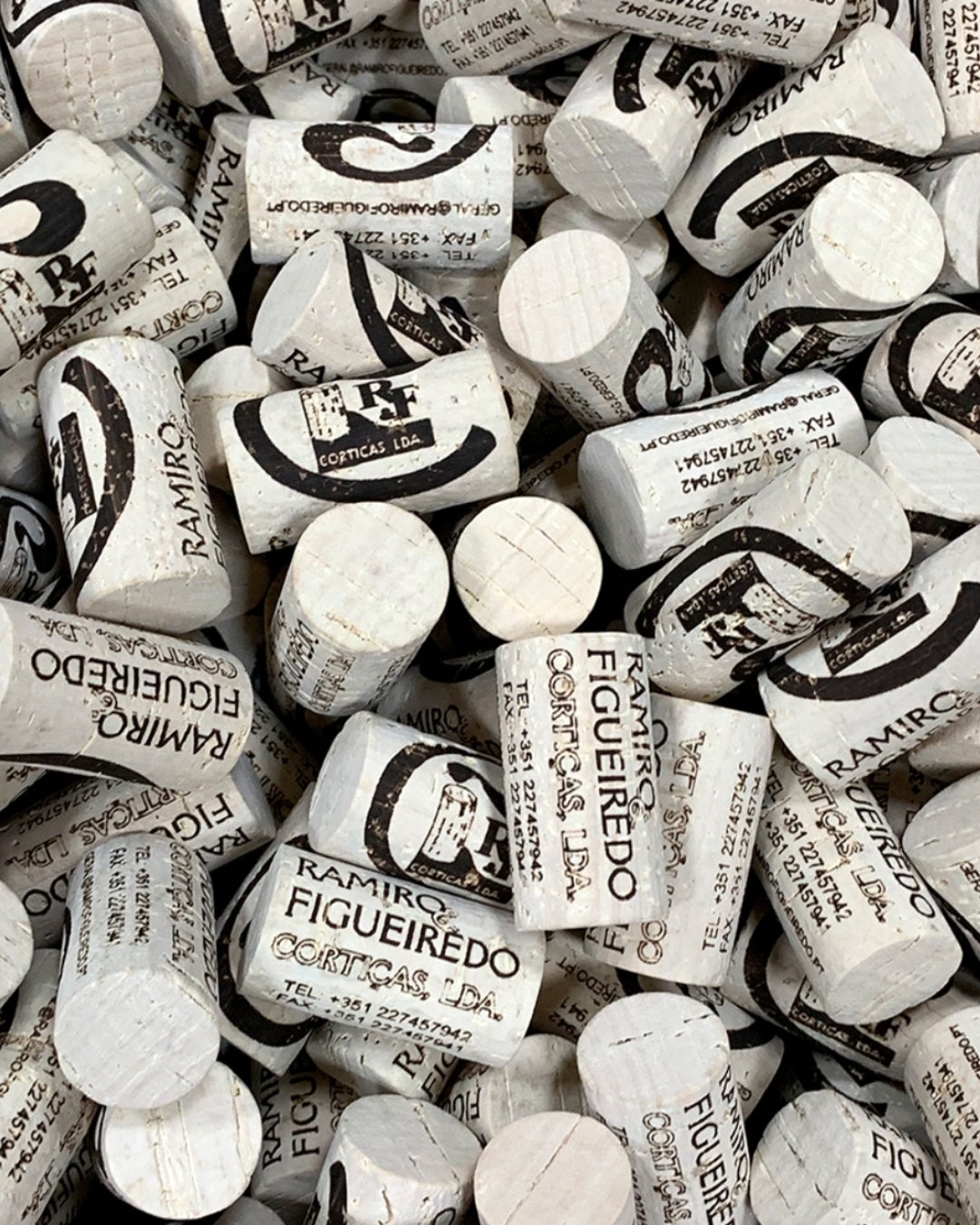
· Dimensions · Moisture · Density · Visual quality · Peroxide content
· Extraction force
· Dust residue · Sealing
· Capillarity · TCA
controls made by RF
Quality by excellence, by meeting all customer, statutory, and regulatory requirements applicable to the products developed and sold by the company.
These are some of the controls carried out by RF to ensure the QUALITY of all its products.